5 Fundamental Practices to Make The Implementation of Warehouse Technology Pay off Big Time.
- bodegasenrenta
- 28 nov 2016
- 3 Min. de lectura
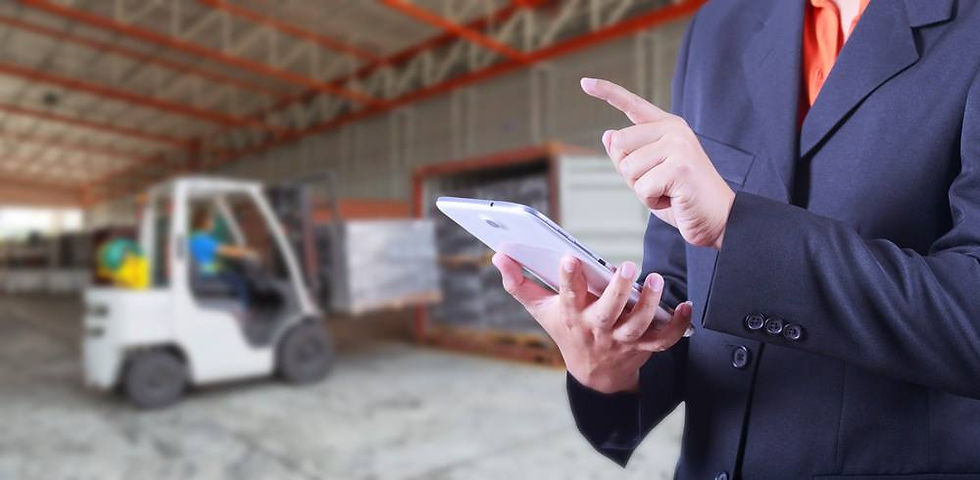
Make Warehouse Process as Simple, Efficient, and Technologically Driven as Possible
Minimizing the steps in the process is a good way to ensure you have a more rapid movement through the warehouse and the freight process. You can benefit from automated packing and shipping processes, such as the use of a transportation management system, for a more efficient outcome and flow around the warehouse on the outbound side of getting out product to your customer. It will take some operational changes and a look at implementation of technology such as ERP, WMS, and TMS, but it will be well worth the effort in the long run. This is especially important when it comes to storage facilities and storage solutions in general.
Technology is Amazing, But Let's NOT Forget the Common Sense Fundamentals to Maximize the Use of Warehouse Technology
1.-Make sure the Warehouse is Aligned to What the Business Wants: Align the operations of your warehouse with the business goals you set in mind when you decided to implement new processes and warehouse technology. Even if you have pressure coming in from your customer base to speed things up, you should still keep your business objectives in mind as well. Find a good balance of action and strategy to ensure you meet both ends of the spectrum for optimum results.
2.-Training: Employees must be trained on procedures, including interaction with the warehouse technology you are implementing such WMS, ERP, or TMS . The excellent manager spends quality time with each team member to coach and encourage him or her. The WMS provides individual performance data to inform the manager as to who needs what specific training. The manager needs to then continually improve using this data.
3.-Employee Motivation: Employee motivation can begin as simply as posting charts of comparative performance to encourage competition. After some data have been collected from the WMS, standards should be established for each warehouse task. Employees who exceed standards can be rewarded informally with perks or specific prizes. Ultimately, a formal gain sharing program can entice an appreciable increase in productivity. Productivity increases of 30% have been reported.
4.-Physical Plant: An excellent warehouse includes adequate dock capacity, ample staging areas, appropriate storage (pallet rack, shelving, flow rack etc.), and suitable equipment (carts, pallet jacks, fork lifts, order picking trucks, etc.). In general, a single level warehouse is preferable, but conveyors and other mechanization can make a multi-level facility nearly as efficient. The excellent warehouse manager plays a proactive role in planning physical improvements.
5.-Automation technology: Of course, fundamentals are exactly what automation is all about. It takes manual tasks, that when executed exactly the same with best practices in mind, can do well, and uses technology to always have the process repeat and scale as expected. This includes vertical and horizontal carousels, conveyors, automatic stacker cranes, automatic pallet wrappers and many other mechanization. The forward thinking warehouse manager will periodically evaluate potential automation projects. The guiding principle here is whether any proposed automation investment in the various warehouse technology available, provides an acceptable financial return. Picking rates using a well engineered bank of horizontal carousels can be three to four times those possible from fixed shelving, transportation costs and resources are now lowered due to less errors, more control, and increased customer happiness....and finally, the accounting department, with great visibility into these processes, will love the new look of a more profitable bottom line.
Comments